Why Traditional Inspection Fails for Next-Gen “Fish-Eyed” Press-Fit Pins — and What We’re Doing About It!
Why Press-Fit?
Automotive systems and servers generate heat, which can build up in an engine compartment or a server module. Press-fit pins provide a reliable interface that naturally dissipates thermal heat, with a significantly higher heat threshold and lower failure rate than solder joints. Another advantage of press-fit over wave-soldered connections is thermal compatibility. If secondary soldering is required, it introduces heat that can damage the PCB and attached electronics. Press-fit technology eliminates the extra heat cycle and allows secondary connections using only force for assembly.
Fish-eyed press-fit pins go a step further, offering superior compliance and retention. The flared structure grips the plated through-hole more securely than traditional press-fit design ideal for vibration, thermal cycling, or heavy data throughput environments. But that complexity comes at a cost.
The Challenge
Traditional 2D inspection systems are not built to handle the complexity of “fish-eyed” press-fit pins, especially in high-density, high-performance connectors like the Next-Gen Paladin HD series, now a staple in today’s complex server boards.
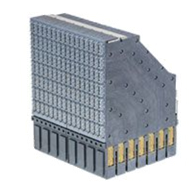
Paladin connectors are a high-speed, high-density interconnect solution primarily used in networking, telecommunications, and data center equipment.
These press-fit pins have a two-part structure: a flexible metal root and a flared pin, forming a shape resembling a fish eye. During assembly, they are inserted into plated through-holes—the pre-seat stage—to prepare for the final press, which ensures mechanical stability and electrical connectivity (after which the board is placed into the server housing for completion of the final assembly).
At the pre-seat stage (the last step before the Paladin components go through a press for the final press-in), the PCB might already have $10K—$15K components placed on it. A single misaligned press-fit pin? That is a failure waiting to happen—if not immediately, then years later when the costly server board is still under warranty. The stakes are high, and hand placement (which is still common!) does not cut it.
Press-fit has many benefits, but the geometry of fish-eyed pins comes with some serious headaches. 👇
Our Solution: Precision 3D Laser Inspection
To solve these issues and ensure consistent quality and repeatability, we have implemented precision 3D laser inspection functionality across our Fuzion™ and Uflex™ platforms (available NOW via RFQ).
This system combines everything required for the successful placement of fish-eyed press-fit connectors:
- 3D upward-looking vision
- Downward-looking PEC camera
- Precision 3D scanning
- Custom vision algorithms
- Tailored nozzles and grippers—designed specifically for your unique component.
This enables us to:
💡 Capture the complete pin geometry, with a clear view of critical lead tips; the system automatically flags and rejects bent or defective pins.
📏 Ensure sub-3μm measurement repeatability, a crucial capability for manufacturers assembling high-value components.
✅ Boost first-pass yield by detecting placement issues early, especially when working with costly parts.
⏱️ Maintain fast cycle times, with inspection adding just 2–3 seconds per placement.
How the System Works
- The Paladin connector is picked from its tray; utilizing a custom gripper
- 3D inspection is performed by the 3D scanner and camera, and confirms 100% lead tip alignment
- 2D inspection is performed by the camera, and confirms board/component alignment
If the pins are straight, and everything is aligned → the part proceeds to placement.
- If not → the part is rejected and returned to the pocket. Our software logs the rejection, captures images, and reports the defects for supplier accountability. This also enables the manufacturer to return the bad part, which helps to save money on these very expensive components.
What are the steps in the inspection process?
- Once the component has been scanned and inspected, it is pressed into the board with 5kg of distributed force using custom tooling that keeps it perfectly parallel to the board. During this process, the fish-eyed pins are inserted cleanly into the pre-drilled holes and held firmly in place. This ensures proper seating during the final press-in—where mechanical and electrical connections are completed.
This press-in method is key for fish-eyed pins, which rely on consistent, parallel insertion to avoid stress fractures or micro-misalignments that could affect long-term reliability.
Want to see a video of the 3D inspection and placement process? Then click on the link below:
https://youtu.be/87yn-hMP5Ms
This system’s precision is critical when placing high-value, high-density Paladin connectors. It’s essentially a “dry run” for component placement—ensuring everything’s aligned and oriented exactly right. You only get one shot, and if you miss, the immediate and long-term cost can be massive.
Contact us to learn more today about this unique solution: https://www.uic.com/contact-us/
📌 Precision matters. Innovation starts at the pin.