Automation is defined as the use of largely automatic equipment in a system of manufacturing or other production process. As with any type of manufacturing process, automated assembly is today’s preferred method to reduce costs as well as increase speed.
What are the benefits and challenges of automation vs. manual processes in PCB assembly? Read on to learn more. . .
PCBs are at the backbone of today’s electronics. It would be impossible to construct computers, smartphones, tablets, or any modern gadget without them. It is therefore vital to have a dependable, strong, and proven method of PCB assembly.
Originally, all PCB’s were assembled by hand, which at the time consisted only of insertion mount components that were generally larger and easy to handle. As the need for accuracy, speed and efficiency increased automated assembly was developed and began to be adopted. Today, electronic parts have gotten smaller and/or or more complex with every advancement, making it very challenging for human assemblers to manually place them accurately and consistently on the board.
Furthermore, today’s manufacturers utilize every inch of the board tightly packing in components. This makes it very difficult to do consistent manual assembly. There just isn’t the room for operator’s hands or fingers to manually place the parts.
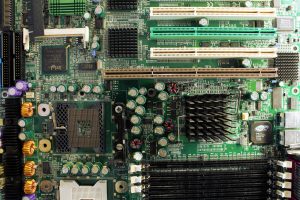
Modern PCB with tightly packed components
Manual assembly requires multiple skilled technicians to do what one automated assembly line can do at a faster rate. There is also a good chance of human error with manual assembly, whereas an automated system will do its job at the same consistent level of quality again and again.
However, manual assembly is still being utilized today for large, heavy and oversized component placement. There are a variety of reasons for this, including:
Perceived Cost of Switching from Manual to Automation
-
Fuzion delivers. . . Less than 2-year ROI
-
Single machine for all odd-form and standard surface-mount; which equates to lower cost
-
Flexibility for widest odd-form part range
-
14 unique grippers/nozzles, 22kg force; industry-fastest odd-form placer
Component Packaging challenges; components are in non-standard packaging
-
We offer the widest variety of high-speed odd-form feeding options, including tape, tube, tray & bulk!
-
Pick your oddest part and we can help you place them!
Reluctance to change established manufacturing processes; tried and true vs. new
-
Automated component placement delivers superior output, yield & quality vs. manual assembly
-
100% pre-insert pin inspection with superior camera vision; eliminates bent or damaged leads for PTH and Press-Fit
Are you still utilizing manual assembly in your PCB manufacturing process? If so, we can help you move towards automation with a variety of solutions.
Below is a case study on how we helped deliver a unique solution to a customer’s placement challenge which helped them automate a manual assembly process and go from 83% to 99% FPY!
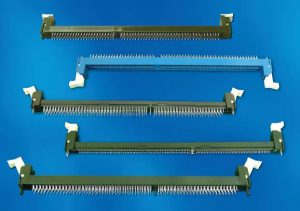
DDR4 DIMM Connectors
DDR4 DIMM connectors, present a unique assembly challenges for the following reasons: First the spacing of the pins is much tighter (DDR3s have 240 pins & DDR4s have 288 – a 20% increase). Secondly, manufacturers have increased the height and thickness to make signal routing easier, and to accommodate more signal layers with the goal of driving more functionality into the same amount of space. As a result, It has become very difficult to accurately place DDR4 connectors by hand, which often result in bending of the pins due to the uneven force being applied by the operator’s hands. Furthermore, due to the location of the connectors, operators are unable to inspect the pins for accurate placement. All of this leads to lower throughput and yield; hence the move towards automated assembly of DDR4 DIMMs.
One of our large customers, a global EMS company, came to us because they were having issues with their DDR4s DIMM connectors which they were placing by hand. Each of the PCBs on their line required the placement of up to 24 DDR4s. They needed to automate this process, and were facing several issues: packaging, placement & component imaging. Here is the solution we delivered to them:
The DDR4 connectors were supplied from their vendor in vacuum-formed bulk packaging. This type of packaging does not allow for a repeatable pick position.
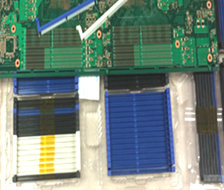
Bulk Packaging of DDR4 DIMMs
Using our in-house 3D printing technology, we conceptualized and created a Matrix Tray Feeder. This solution allowed the DDR4 connectors to be consistently fed into their Fuzion machine.
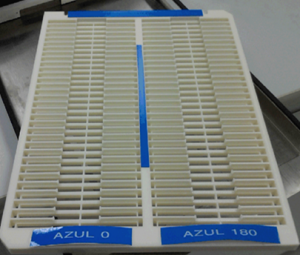
Custom 3D Printed Matrix Tray Feeder
The extreme length of the connector (5 1/4”) was causing warping during placement because the force was concentrated in the middle causing miss-insertions. To solve this, we developed a new Gripper and Adaptor which stabilized the connector – see this in action in the video clip below.
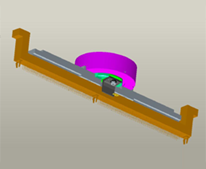
New Custom Gripper & Adaptor
We also modified the FZ7™ head to use 3 spindles to place it allowing for higher gripping force. And, we added heavier springs to compensate and adjust for touchdown sense. This solution eliminated the miss-insertion issues altogether!
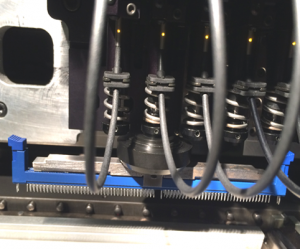
3 Spindle Connector Placement
Lastly, the finishing and color of the leads on the connector also caused machine imaging problems. We created a new machine algorithm and designed a cover with a square notch for the Magellan® camera. This forced the vision inspection system to see the lead tips only, allowing for imaging of 100% of the leads.
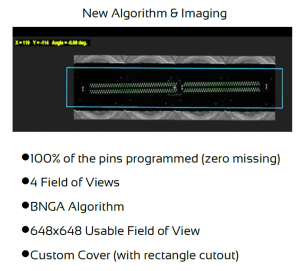
Side note: Our customer found this solution so robust, they are using the vision system to quality inspect incoming DDR4s, and are using it to reject non-conforming parts. This has resulted in a further cost savings for them!
Click here to see a video of our DIMM Connector solution in action!
This Unique solution allowed our customer to efficiently switch from manual to automated assembly for their DDR4 connectors. It also increased their first-pass yield from 83 to 99% FPY, which resulted in a very happy customer!
Like what we did? We can help YOU automate your manual PCB assembly processes. Reach out and let us know how we can help!
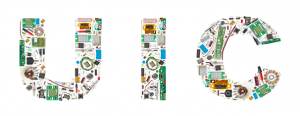